【物流作業改革】第41回 倉庫レイアウトの問題点把握
2013年3月18日
物流作業改革の検討をする場合、倉庫レイアウトの視点で検討をすると数多くの問題点を見つけることができる。問題を見つけ出す一番のポイントは、1日の業務の流れを頭の中に描きながら人をレイアウト上で動かしてみることである。今回は、倉庫レイアウトの視点での問題発見手順を述べたい。
まずは、在庫エリアの視点。ピッカーの作業効率を考えた場合、「5つの無駄(待つ無駄、考える無駄、移動する無駄、探す無駄、取る無駄)」を改善できれば作業効率が上がることは以前述べた。在庫エリアにあてはめてみた時、「通路のすれ違い待ち」「移動距離の長さ」に着目すればよい。ピッキングリストを発行するプリンタが、ピッキングのスタート地点である(図の右中央)。在庫エリアの右半分によく出る商品が集中していれば移動する距離が短くなるため、ピッキング効率が向上する。そこで今の在庫配置が、どの様な順番で行っているかを確認する。仕入先別に在庫配置をしているのであれば、あまり出荷されない商品も混在しているため、出荷効率が悪い可能性が高いと思われる(詳細は後の号で述べる)。商品カテゴリ別の在庫配置も同様である。ゴールデンエリア(出荷多頻度商品、出荷大量商品)、出荷極小エリアを設けていなければ効率が悪いと考えてよい。また通路幅が狭く、ピッカーのすれ違い待ちが発生していたり、通路が行き止まりになっていれば歩く距離が長くなるため、作業効率は落ちてしまう。
おそらく、皆様の物流センターの在庫エリアにこの考え方を取り入れた場合、「商品を置く場所が無くなる」「入荷効率が悪くなる」と反論する方もおられると思う。しかし、対応策はいくらでもあるので、問題点の抽出時点では考えないで欲しい。
次に作業エリアの視点。ピッキングが完了すると、検品待ちエリアに商品を置く。流通加工(値札貼り、セット組み、袋詰め等)を行ってから検品エリアに移動し、出荷検品・梱包を行う。運送便の送り状・荷札を添付した後に、運送会社別の仮置きエリアに移動する。この様な作業スペースは広すぎても、狭すぎてもいけない。それぞれの作業効率目標から算出して人の配置を行い、作業区別の適正人数から作業スペースが算出される。この様な視点で考え、物流の流れがスムーズになっているか(交錯していないか、移動距離が短いか、商品の滞留は無いか)を議論すれば、問題が見つかるものである。
このコラムは大塚商会様のERPナビにて連載中のコラムを並行掲載しているものです。
新刊のご案内:2014年7月
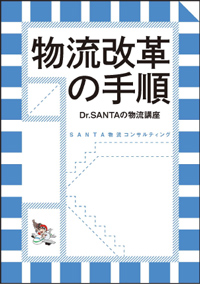
物流改革の手順(出版文化社)
1,890円
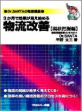
3ヶ月で効果が見え始める物流改善
【現状把握編】
(プロスパー企画)
1,890円