【物流クレーム改革】第35回 商品違いの改善
2013年3月18日
物流クレームの中で最も多い現象は「商品違い」である。商品違いの対策として「ピッキングする時に正確に確認する」が多いのには驚く。誤出荷をした本人にとっては、「正確に」とはどういう確認の方法をすればよいのかはっきりしない。明確な対処方法が無いのであれば、当然のことながら同じミスを繰り返すことになるのである。
ピッキングリストで出荷をしている運用を例に挙げて解説する。ピッキングリストに印字されている項目として、「商品コード」「商品名」「数量」がある。ロケーション管理をしている企業は、この項目に加えて「在庫ロケーション」が印字される。ピッキング時に確認する項目は企業によって若干変わるが、基本的には「商品名」と「数量」を確認した上で、ピッキングリストの各明細に「レ」をチェックする。取扱い商品によっては、商品の「サイズ」や「材質」が間違い易いため、「商品名」「サイズ」「材質」「数量」の4点をチェックをしていることもある。
まずは、このチェック方式を定着化させることが先決となる。チェックをすることにより、「間違っていないはず」という思い込みを極力排除させるのである。物流マネージャーは、1日の終わりにピッキングリストにざっと目を通し、ピッキングリストの所定箇所にチェックが入っているかを確認する。ピッキングリストに「ピッカー名」「検品者名」を記入していると思われるので、抜けが多い人にはチェック方法の指導を個別に繰り返す。しかし、この運用を続けているうちに、ピッキングリストにチェックをしているが確認作業をしていない人が出てくる。これは、物流マネージャーがチェックすることだけを強く言うため、「確認することが目的」から「チェックすることが目的」になってしまうからである。目的を説明した上で指導をする方法を是非とって欲しい。
しかし、このチェック方法だけでは商品違いは無くならない。「?ピッキングリストと現物商品の商品名が違う」「?入荷時の棚への入れ間違い」「?棚の中で山崩れが発生し、違う商品と混ざる」「?返品後の棚戻し間違い」が発生するからである。
?の商品名が違う問題は、現物商品名を商品マスタに登録するだけで単純に解決できる。ただ、「商品マスタの桁数制限」「商品名の統一ルールが無い」「現物に商品名が書いていない」等、難題をかかえている企業も少なくはない。この場合は、「商品名でなく、ロケーションでピッキングする」「商品名を入荷時に紙などに印刷し、商品や棚に貼る」等、運用の見直しを行わない限り商品違いは少なくならない。
また、違う商品を置いている問題は、「棚入れ間違いを減らすための入荷作業の運用」「山崩れ防止の仕切り板の導入」「物流クレーム改革による、誤ピッキング返品棚戻しの削減」を行う必要がある。
これに加え、「間違い易い商品の棚に注意札を貼り付ける」「検品者の強化(商品違いが多いピッカーの検品強化、商品違いが多い商品の検品強化)」「新人への教育体制強化(物流クレームの現象の説明)」「バーコード検品システムの導入」等、取り組むべき事は多い。
このコラムは大塚商会様のERPナビにて連載中のコラムを並行掲載しているものです。
新刊のご案内:2014年7月
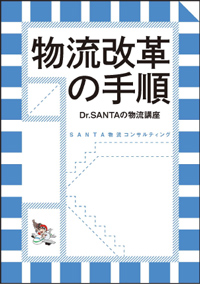
物流改革の手順(出版文化社)
1,890円
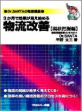
3ヶ月で効果が見え始める物流改善
【現状把握編】
(プロスパー企画)
1,890円